Chip Sharing in Logistics: One RFID Chip for All
SCHREINER LOGIDATA
Chip Sharing in Logistics:
One RFID Chip for All
In logistics and assembly processes, for product marking and in the service sector: RFID technology has been gaining increasing traction in recent years. RFID is particularly important in tracking returnable transport items in logistics, in connected manufacturing applications and in processes with high quality or documentation demands. Chip sharing offers a sustainable and therefore cost-efficient solution for all of these purposes. Frank Linti from the Schreiner LogiData competence center explains details, aspects that need to be considered and the benefits this concept offers.
In the first stage of an RFID project, some general questions are addressed and answered: What products should be identified? What processes are related to these products? What content should be stored on the label? Especially the selection of the number sequences to be used is very complex in many applications. Too much information on the RFID label reduces bulk reading speed and frequently results in a confusing data construct. By contrast, too much unused storage capacity on the RFID label is uneconomical.
Important: Looking at the Whole Supply Chain
In the RFID planning stage, it’s important to look at all the stations an item will pass through—in other words, not just internal checkpoints but also in the operations of suppliers, assembly plants or logistics service providers (LSP). In times of increasingly shorter product lifecycles and growing numbers of variants, rigid, high-volume manufacturing processes are no longer in demand. Flexible systems offer a major advantage here.
Example: Machine Manufacturers
Manufacturers of high-end machines are a good example of why the entire process chain always has to be looked at: Various suppliers assemble machine components from parts supplied to them by their suppliers. As early as in that stage, end-to-end component data acquisition and documentation takes place: partially automated and partially through manual barcode reading. Following assembly and quality inspection, the components and their pertinent data are handed over to logistics service providers that have to forward the units just-in-time to the intralogistics department of the machine manufacturer’s designated plant. There, the items are captured in the receiving department, posted to the kanban system and placed into intermediate storage until the manufacturing sequence requires the parts. The components are captured once again and staged at the assembly line, where they’re read in at the time of installation and posted to the machine.
Benefit: Chip Sharing
RFID technology offers numerous opportunities for shared utilization of a label across all applications. This yields the highest economic benefit and massively enhances processing speed, communications and reliability. In chip sharing, the basic blocks to be programmed are defined on the chip once. This is the content the machine manufacturer will read across its own process. All other blocks are divided and allocated to the users within the chain, which defines the places in which data can be moved. These blocks are written to, disabled and read only by the relevant partner, but not by the manufacturer in its standard processes, which ensures fast bulk reading in logistics operations. In spite of this sharing concept, all parties have access to a single data storage medium.
Chip sharing projects: Schreiner LogiData provides advice
The utilization of a high-end RFID chip and a high-quality, long-lasting RFID label is important in this context because the data should remain readable by distributors or directly by the end user in the event of product returns. The HFand UHF-RFID labels that have been in worldwide use to date operate within standardized ISO structures, which makes them suitable for global utilization across the entire user chain.
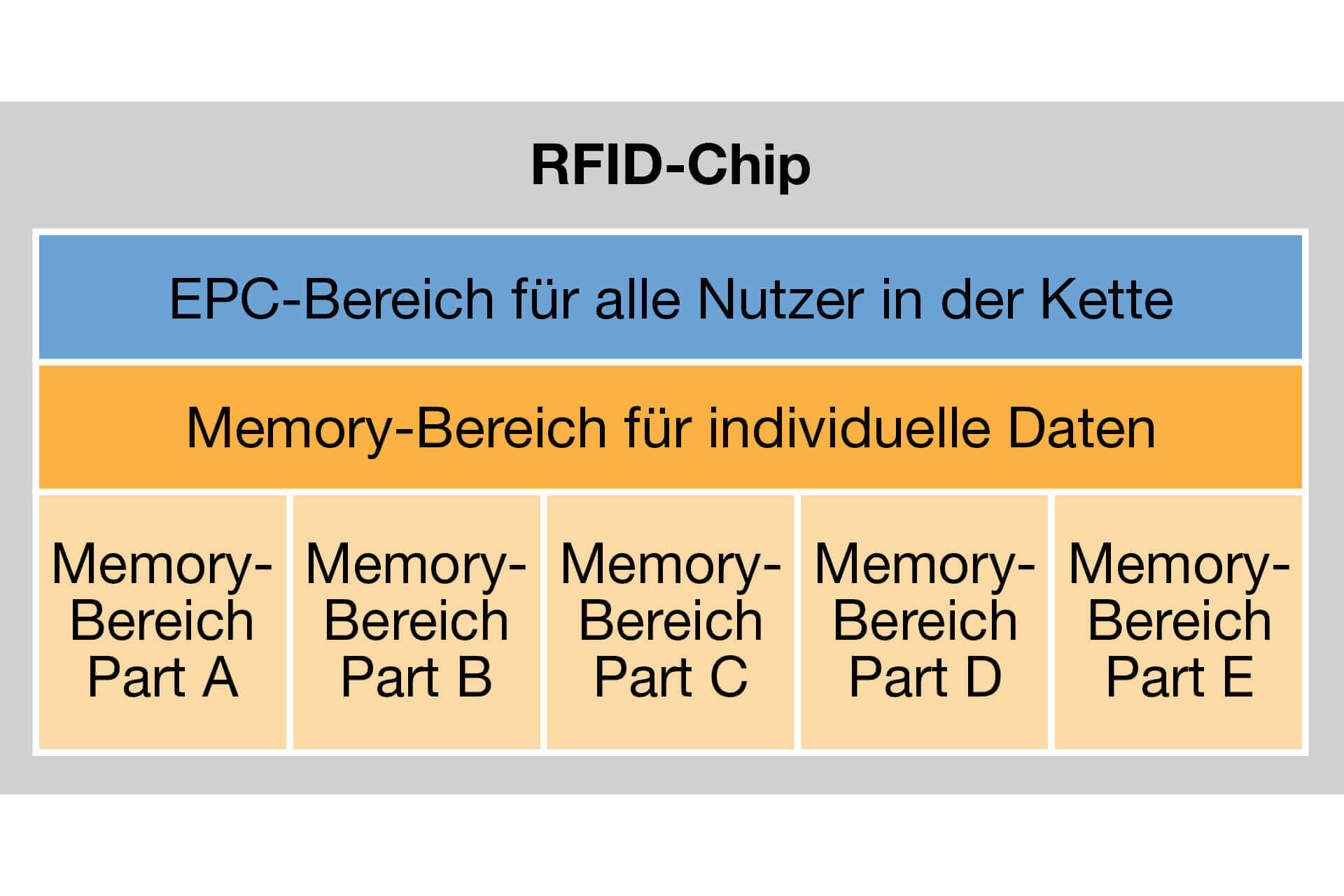