A Race Against Time
SCHREINER PROTECH
A Race Against Time
The first 20 minutes folllowing the descent of an avalanche are crucial for rescuing people buried in the snow. Their chance of survival drops rapidly after that. Avalanche transceivers such as Mammut’s Barryvox high-tech tool help find buried alpine athletes quickly. An extremely robust housing and Schreiner ProTech’s Pressure Compensation Seals (PCSs) ensuring venting of the transceivers while preventing moisture ingress provide adequate protection of the complex electronics in a Barryvox.
When every minute counts the combination of innovative technology and ease of use enables short search times. Mammut’s Barryvox is the first avalanche transceiver with an integrated 360-degree direction indicator and has already been recognized with the ispo Outdoor Award and the Volvo Design Award. To ensure perfect performance, the highly complex electronics have to resist adverse conditions. The avalanche transceivers have to be fully functional at all times, without waiting periods, at temperatures down to – 20 °C, and up to 15 cm under water.
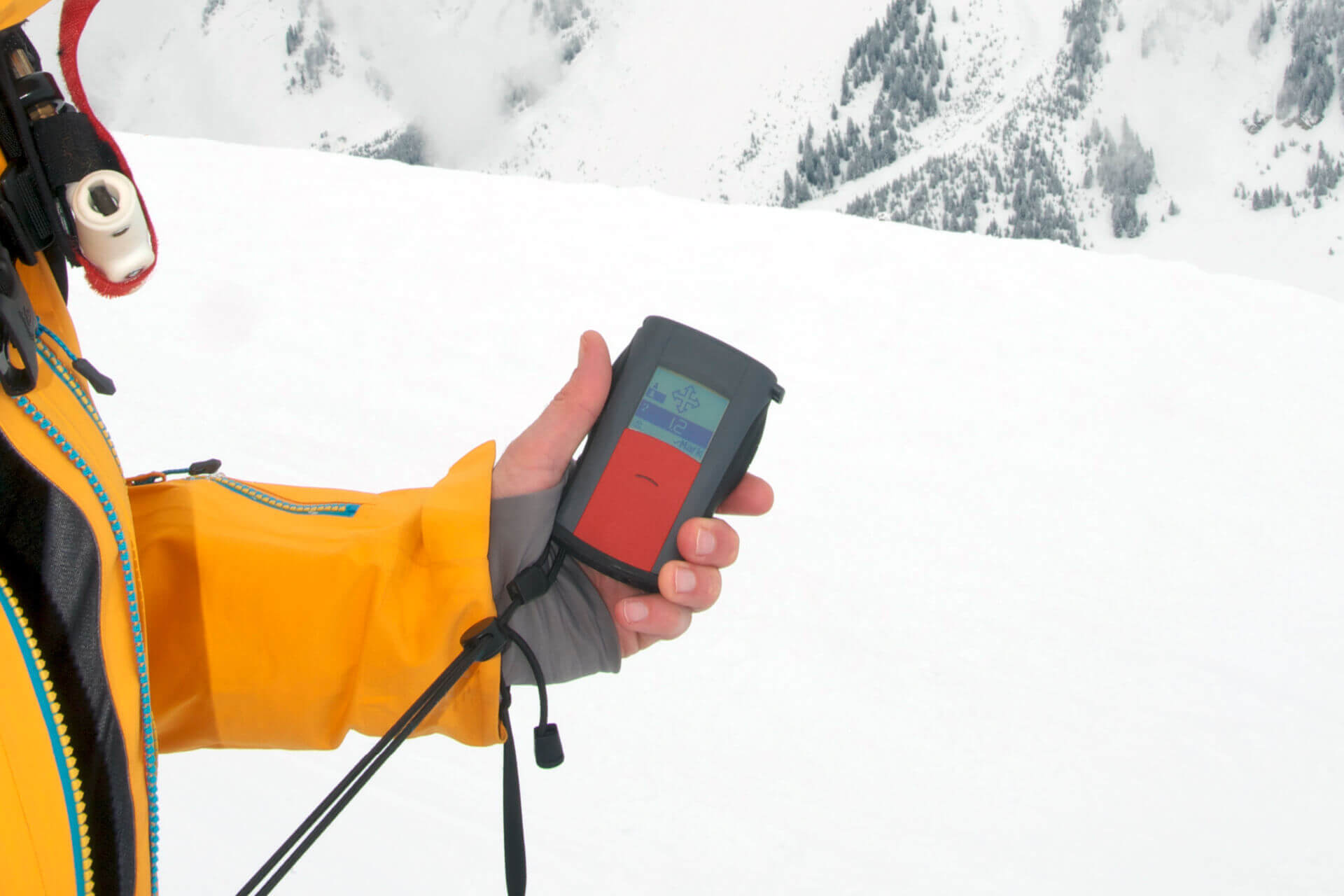
Absolutely Watertight and Shockproof Housing
A rapid change in temperature or elevation above sea level—for instance during heli-skiing or fast downhill runs—may lead to pressure differences that impair the performance of the loudspeaker’s membrane, resulting in malfunction or damage. Appropriate pressure compensation is required to prevent this.
Pressure Compensation Seals: Air Yes, Moisture No
For reliable performance of the avalanche transceivers, venting must be ensured while ingress of moisture and dirt must be prevented. For air exchange and pressure reduction inside the Barryvox housing, Mammut uses the Pressure Compensation Seals from Schreiner ProTech. “The Pressure Compensation Seals prevent excess pressure inside the electronic housing and are totally impermeable to water due to their special membrane,” says Senior Product Manager PCS Adrian Marggraf from Schreiner ProTech.
For application in the avalanche transceiver based on the customer’s information, the optimal membrane design was established using a calculation model. The type of material and surface quality of the housing were decisive for selecting the suitable adhesive. “We offer our customers individual supporting services in all development stages—from component design through to validation and application—and are on site during the integration stage into the production process. That means we also take care of training, maintenance, and repairs of the processing systems,” adds Marggraf.
Stress Tests Successfully Passed
To validate the Pressure Compensation Seals, the device was placed 15 cm under water in a defined immersion test simulating a dive in a mountain creek. For a few days, the Barryvox was stored at 95 percent humidity. Following these tests, the mechanical stability of the membrane was checked. The membrane and the adhesive fully resisted the mechanical pressure increase. Adhesion proved to be very good also in tampering attempts using a sharp knife and flat-nose pliers. At Mammut, the Pressure Compensation Seals are applied using a tool specifically created for this purpose. The upper part of the Barryvox is prepared for final assembly and the Pressure Compensation Seal is subsequently pressed on.
For Mammut, the Pressure Compensation Seals provide a cost-efficient means of supporting reliable performance of the Barryvox avalanche transceivers. As a result, users can be sure that the avalanche transceivers function even in conditions of heavy snowfall, rain, and moisture.